
What is Distributed Control System (DCS)?
Introduction to Distributed Control System (DCS)
A Distributed Control System (DCS) is a control system that is distributed throughout a network, using components that are located near the controlled process or system. In recent years, the prevalence of smart devices and field buses has made DCS more prevalent in large and complex industrial processes, as opposed to the previous centralized control systems. This shift allows for greater efficiency, reliability, and flexibility in controlling and monitoring industrial processes.
Advantages of using Distributed Control System (DCS)
- Increased reliability due to redundant components spread throughout the network.
- Scalability to accommodate varying process sizes and complexities.
- Enhanced flexibility in configuration and control of processes.
- Improved maintenance and troubleshooting capabilities.
- More efficient monitoring and data collection for analysis.
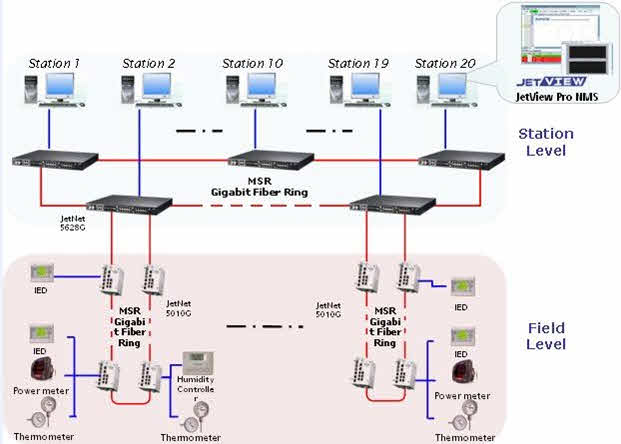
Key Components of DCS System
Geographically distributed control elements
A Distributed Control System (DCS) comprises control elements distributed geographically across the plant or control area, allowing for efficient monitoring and control of industrial processes.
Integration of advanced control strategies
DCS integrates advanced control strategies for optimizing manufacturing processes, ensuring seamless automation and efficient operation. The system organizes the control structure into a unified automation network, enhancing coordination and information flow between subsystems.
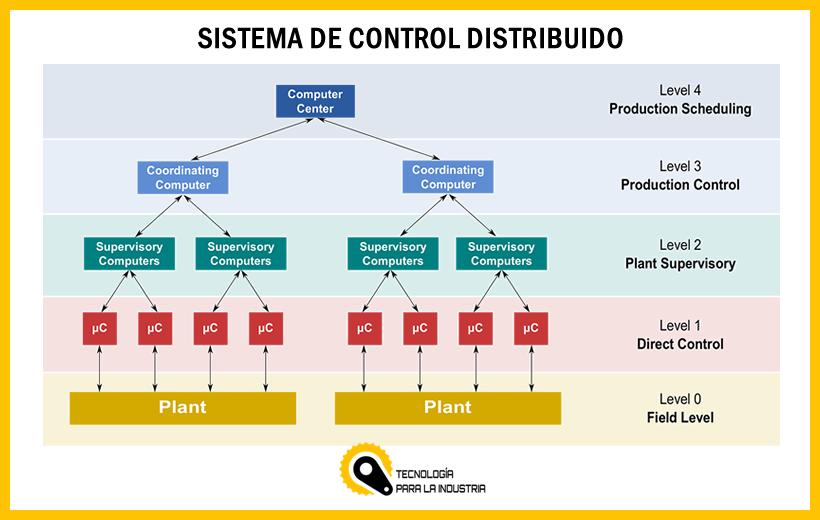
Applications of DCS in Various Industries
Chemical plants and oil & gas industries
DCS systems find extensive application in chemical plants and oil & gas industries due to their ability to monitor and control complex processes efficiently. The integration of control elements distributed geographically enables real-time oversight, enhancing operational safety and productivity.
Food processing and nuclear power plants
In the realm of food processing and nuclear power plants, DCS plays a crucial role in ensuring precise control and monitoring of critical operations. The utilization of advanced control strategies elevates process efficiency and accuracy, contributing to streamlined production and heightened safety protocols.
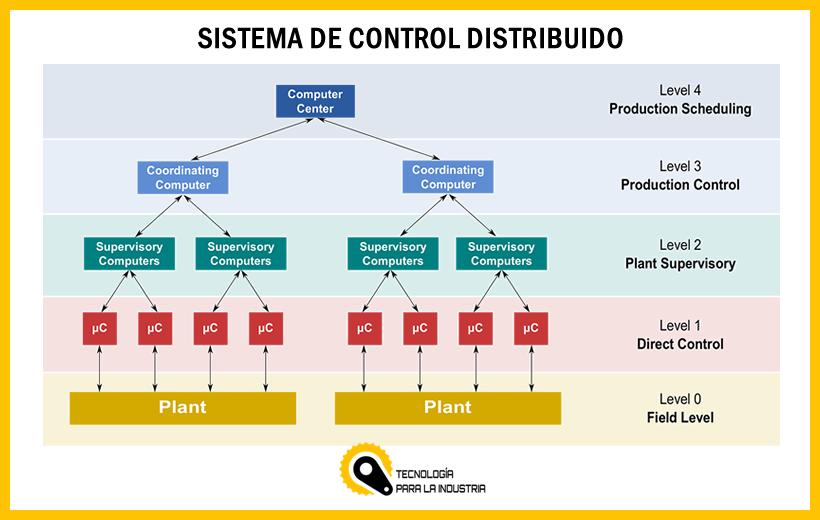
How DCS Enhances Plant Efficiency
Efficient ways to improve control and process quality
DCS systems facilitate the enhancement of control and process quality in various industries. Through the utilization of advanced algorithms and real-time monitoring capabilities, DCS enables precise control over critical operations, leading to enhanced process efficiency and reduced errors.
Reliability and efficiency in plant operations
In plant operations, DCS plays a crucial role in ensuring reliability and efficiency. By centralizing control functions and providing real-time data analysis, DCS allows for quick decision-making, proactive maintenance, and improved overall operational efficiency. This leads to minimized downtime, streamlined production processes, and optimized plant performance.

Evolution of Control Systems: From Centralized to Distributed
Transition from centralized control to distributed control system
DCS systems have revolutionized industrial processes by shifting from centralized control to a distributed architecture. This transition enables enhanced flexibility, scalability, and resilience in managing complex operations across various industries.
Benefit of distributed control architecture in industrial processes
Distributed control architecture offers numerous benefits in industrial settings. It provides increased reliability, efficiency, and real-time monitoring capabilities, empowering organizations to optimize production processes and minimize operational risks. The decentralized approach of DCS enhances plant performance and ensures seamless integration of smart devices for improved control and process quality.